- Kategori
- Lojistik / Taşımacılık
Yalın Lojistik Depo Prensipleri
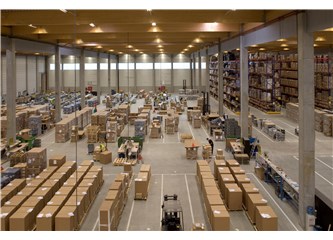
Bir çok farklı şekilde tanımlansa da, lojistik; bilginin ve fiziksel ürünlerin ‘Tedarik + Malzeme Yönetimi + Dağıtım’ aşamalarının yönetilmesidir, diğer bir deyişle ürünün üretim aşamasından nihai tüketiciye ulaşmasına kadar olan süreçleri kapsamaktadır.
Lojistik maliyetleri incelediğimizde de şu şekilde bir tablo karşımıza çıkmaktadır, depolama ve stoklama giderleri %35 lik bir paya sahiptir.
Sevkiyat |
%45 |
Depolama |
%25 |
Yönetim Giderleri |
%10 |
Stoklama Maliyetleri |
%20 |
|
%100 |
Yönetim giderleri değerlendirmeya almazsak yaklaşık %50 gider payına sahip depo yönetimine hak ettiği önemi verdiğimizi düşünmüyorum.
Klasik Lojistik depoların gider maliyetlerine göz atacak olursak; en yüksek giderin iş gücü olduğunu görmekteyiz.
Depo Giderleri | Oran |
İş Gücü | 50% |
Bina | 25% |
Bakım ve Servis | 15% |
Ekipman | 10% |
Toplam | 100% |
Depolarda gerçekleştirilen ana faaliyet ve iş süreçleri şunlardır; Teslim alma, İç Transfer, Stoklama, Sipariş toplama, Sınıflandırma- birleştirme, Sevk etme, Çapraz sevkiyat, Paketleme, Etiketleme, Adresleme, Paletleme, Diğer katma değerli hizmetler.
Bu faaliyetlerin yerine getirilmesi anlamında Lojistik ve Tedarik zinciri yönetiminde önemli bir süreç olan depo yönetimi mevcut teknolojik gelişmelere rağmen sektör olarak çoğu lojistik firmasının bu gelişmelerin gerisinde kaldığı , geliştirme ve iyileştirme çalışmalarına çok fazla önem vermediğini görmekteyiz. Daha çok işgücüne dayalı çalışan depo operasyonlarında maalesef amaçlanan verimlilik artışı gerçekleşmemektedir.
Depolama faaliyetlerinin ana amaçları
· Depo stoklama alanının optimize edilerek maksimum seviyede kullanılması
· Depo ekipmanlarının optimize edilmesi
· Depo personelden en verimli seviyede faydanılması
· SKU elleçlemelerin azaltılması, gerekli SKU erişilebirliğinin sağlanması
· Şirket operasyon giderlerinin azaltılması olarak özetleyebiliriz.
Peki bu kadar önemli amaç ve süreçlerin gerçekleştirildiği depolarımızda nasıl başarıya ulaşacağız, maliyetlerimiz nasıl azaltacağız ve aynı zamanda da hizmet-servis kalitemizi de artıracağız? Bu hedefleri başarmak için 1940 lı yıllarda Japonya’da kökleri atılan yalın düşüncenin Toyota’da uygulanmasıyla ortaya çıkan verimlilik artışının nasıl gerçekleştiğini incelememiz gerekiyor.
Yalın üretimde, gereksiz faaliyetler yani israflar 3M terimiyle tanımlanır. 3M terimi Japonca’da M harfi ile başlayan üç kelimenin baş harflerinden meydana gelmiştir. Bu kelimeler muda, muri ve mura olarak sıralanabilir. Bu kelimelerin ifade ettikleri anlamlar şöyledir :
u Muda : Kayıp anlamına gelir. Yapılması halinde ek bir fayda sağlamayan işlemlerdir.
u Muri : Aşırı yük anlamına gelir. Çalışma alanında bulunana ekipman ve insanların normal kapasitelerinin üzerinde çalıştırılarak zorlanmaları olayıdır.
u Mura : Düzensizlik anlamına gelir. Çalışma alanındaki işi engelleyen veya zorlaştıran her türlü düzensizliklerdir.
Yalın düşüncenin ana fikri israflardan kurtulmak ve arınmaktır(Muda) ve bu bağlamda 7 tane israfı anlamamız ve tanımlamamız gerekiyor;
1) Taşıma : Ürünlere herhangi bir katma değer sağlamayan ve/veya müşterinin karşılığını ödemediği, ürünlerin ve çalışanların hareketlerine işaret etmektedir. Bu israf hareketleri tamamen elimine edilememesine rağmen sürekli olarak azaltılabilir. Ayrıca yüksek seviyede ürün hareketi de hasar ve ziyan riskini artırmaktadır.
2) Stok : Fazla ürün stoğunun tutulması daha fazla depo alanı, daha uzun sürede ürün toplama demektir ve en önemlisi firmanın yeni ürün yatırımını azaltmaktadır. Bu israfları önleme prensibi tam zamanında(JIT) ürünleri ihtiyac olduğunda tedarik etmektir.
3) Hareket : İnsan ve makina hareketlerinde israfı engellemek için fonksiyonel ergonomik çalışma alanının yaratılması gereklidir.
4) Bekleme: Ürünlerin biriktiği ve işlem görmek için beklediği israf zamanıdır. Bu aşamada ürün firma ve/veya müşteriler için hiç bir değer yaratmamaktadır.
5) Fazla Üretim: En ciddi israf ve bir çok problemin ana nedenidir. İhtiyaçtan fazla üretilen ürün gerekenden fazla hareket israfına neden olacak, stok artacak ve esneklik gücü azalcaktır. Çekme prensibi aşırı üretimi engellemede efektif bir yöntemdir.
6) Aşırı Süreç: Büyük makine ve ekipman kullanımında oluşan israflardır. Daha ufak, ucuz ve esnek makineler temin edilerek sürekli kullanılmalıdır.
7) Hata ve Sapmalar: Hataların anında saptanması önemli ve hemen çözülerek ürünün değerini kaybetmesi engellenir.
Yukarıda belirttiğimiz israfların, lojistik depolarımızda verilen hizmetlerin tüm süeçlerinin bu 7 israf unsurları dikkate alınarak süreçlerin yeniden incelendikten sonra değerlendirilip tüm israfların ortadan kaldırılması ve minimize edilmesi gereklidir. Bu amaca ulaşmak için depo içerisinde uygulanabilecek yalın yönetim prensiplerinden bir tanesi de 5Suygulamasıdır ve yine çalışma ortamında düzen ve tertip getirerek, gereksiz ekipman ve hareketleri minimize ederek zaman israfını azaltmayı amaçlamaktadır.
1) Seiri (Sınıflandır)Çalışma alanında anlık ihtiyacı duyulmayan malzeme, ekipman ve aletlerin sınıflandırılarak ilgili bölgeden uzaklaştırılmasıdır.
2) Seiton (Sırala / Düzenle) Sürekli ihtiyaç duyulan ekipman, demirbaş vb. malzemelerin bulunmasını ve kullanılmasını kolaylaştırmak amacıyla yapılan dizme, düzenleme ve tertip işidir. İyileştirme projesi her türlü alet, aparat ve makinayı kapsar.
3) Seiso (Sil / Temizle) Çalışma alanlarında ve makinelerde çevre, üretim ve makine kaynaklı her türlü kirliliğin yok edilmesi ve korunmasıdır. Temizlik aynı zamanda duyu organlarımızla yapabileceğimiz bir kontroldür, oluşabilecek hataları önceden tespit etmemizi sağlar.
4) Seiketsu (Standartlaştır) Toparlama, düzen ve temizliğin korunması ve sürekliliğin sağlanması için oluşturulması gerekli standartlar, kontroller ve iyileştirmelerdir.
5) Shitsuke (Sahiplen / Sistemi Koru) Mevcut adımların sürekliliğini sağlamak, çalışanları eğitmek, iyileştirmeleri duyurmak, sloganları bulmak, kampanyalar yapmak ve takımları ödüllendirmektir. Başka bir deyişle, 4 adımı birbirine bağlayan çalışmadır.
Yalın Yönetim uygulamaları ile mevcut ve yeni kurulacak bir lojistik depo iş süreçlerinden israfları minimize ederek, sürekli iyileştirme çalışmarını sürdürürek verimliliği artırabilirsiniz ve üstüne basa basa belirtmem gereken en önemli unsur olan insan faktörüne ayrı bir önem göstermeniz ve çalışanlara sürekli eğitimler vermeniz gerekmektedir.
Daha sonraki paylaşımlarımda daha detaylı bilgilerle buluşmak üzere, saygılarımla.
Barış Akçay